Technologies
Accelerating the industry transformation with proprietary technology
As an innovation leader Borealis continues to develop its portfolio of proprietary technologies while building on the achievements and experience of more than 50 years in the industry. Through its joint ventures, Borealis keeps discovering new, innovative ways of creating next-generation, value-creating products to meet customers' needs on a global scale.
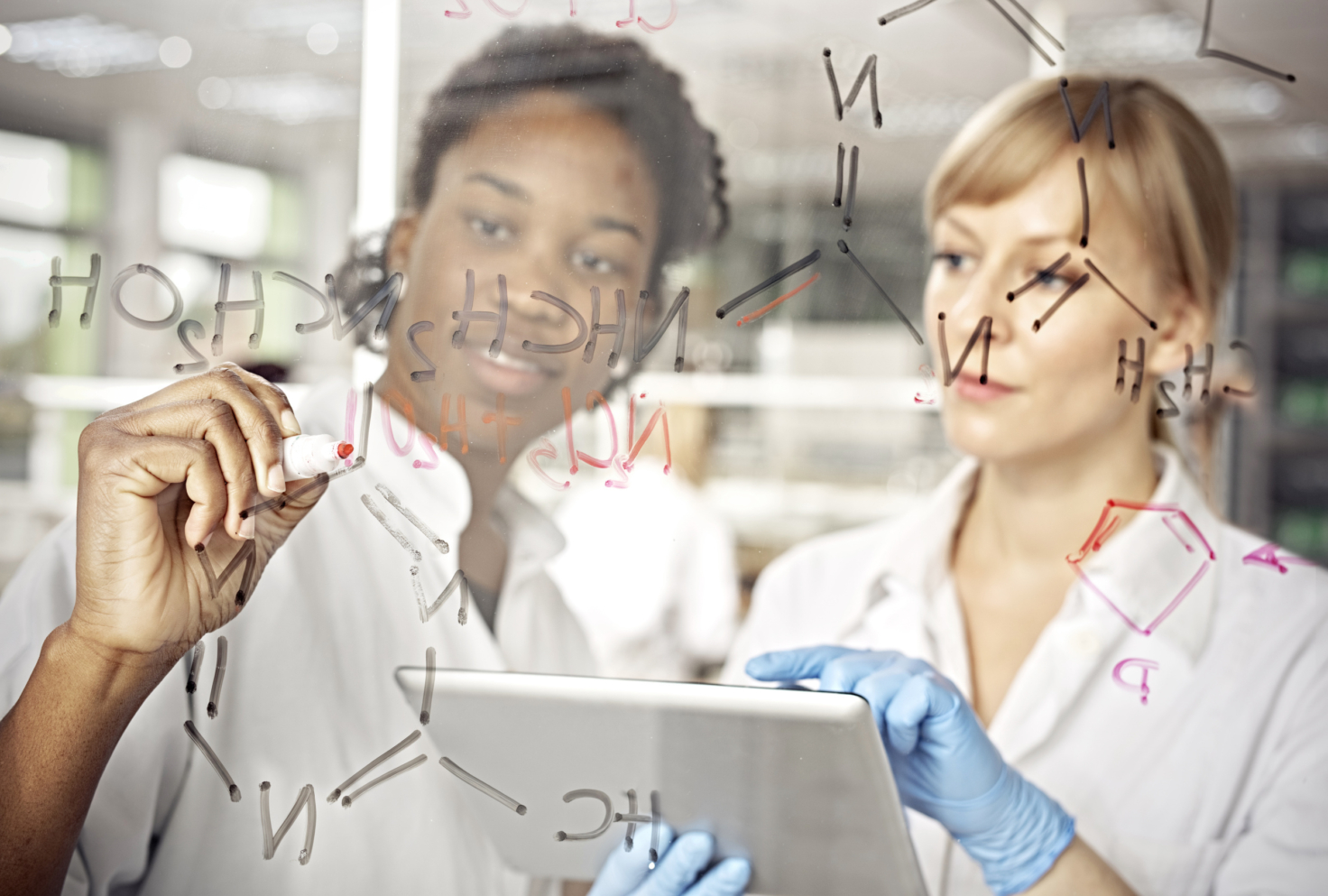