Consumer Products
Making everyday life easier
Explore our sustainable polyolefin solutions designed to meet a wide variety of household needs. Created using proprietary technologies, this advanced portfolio provides the optimal balance of functionality and quality for applications including advanced packaging, technical fibers, white goods, and small appliances.
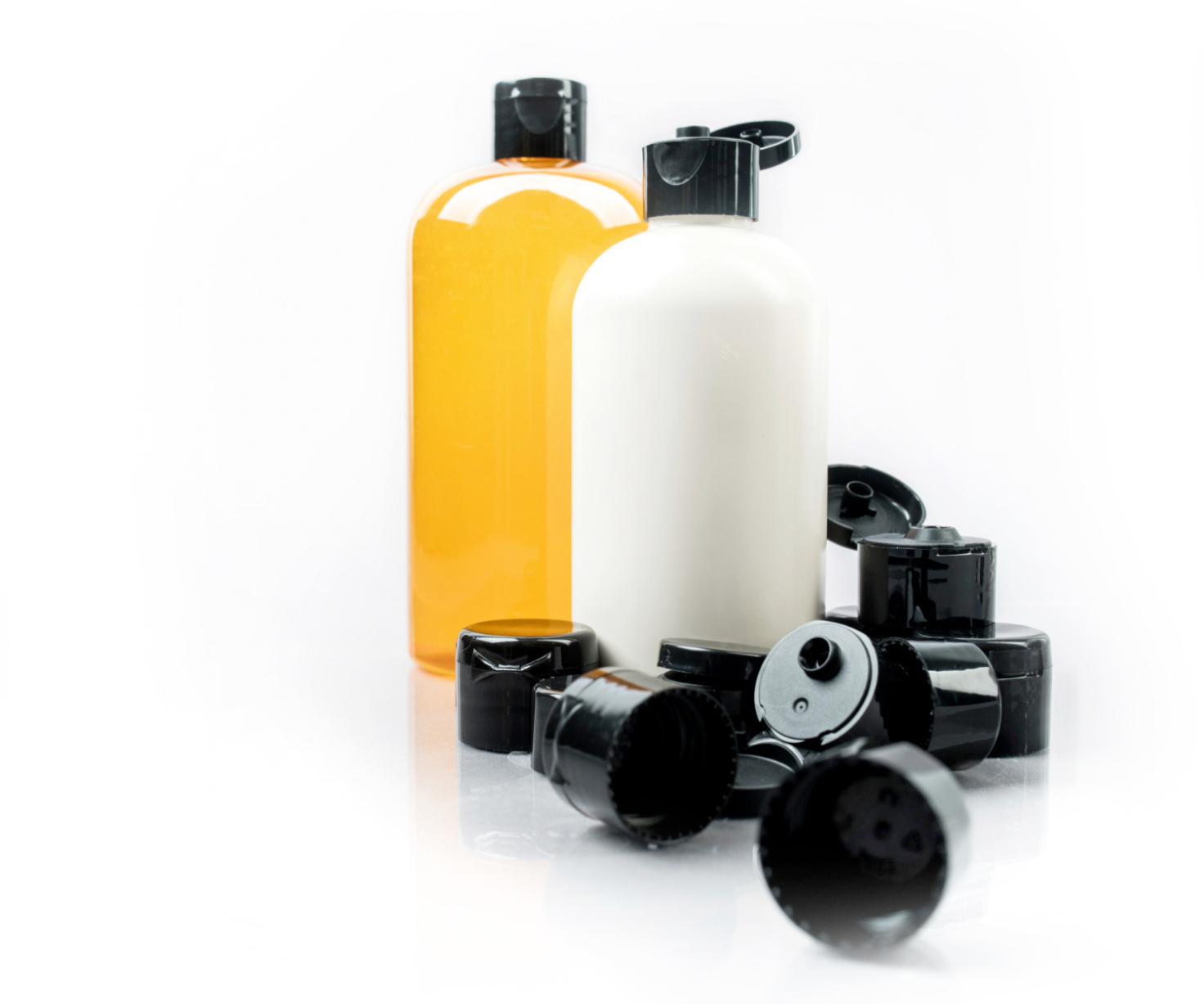
Applications
Create visually appealing appliances that stand out in the market, with our grades that offer design freedom, outstanding performance, and sustainable content.
Effective solutions suitable for a broad range fiber applications, based on reliable, high-performance grades.
Advanced flexible packaging that helps protect and preserve food, avoids spoilage, and keeps products fresher for longer.
A range of superior rigid packaging solutions that balance cost and performance, continually enhanced in collaboration with our value chain partners.
Appliances
Create visually appealing appliances that stand out in the market, with our grades that offer design freedom, outstanding performance, and sustainable content.
Fibers
Effective solutions suitable for a broad range fiber applications, based on reliable, high-performance grades.
Flexible Packaging
Advanced flexible packaging that helps protect and preserve food, avoids spoilage, and keeps products fresher for longer.
Rigid Packaging
A range of superior rigid packaging solutions that balance cost and performance, continually enhanced in collaboration with our value chain partners.